Industry 4.0 is upon us but the manufacturing workforce is struggling to keep up. Here’s the solution.
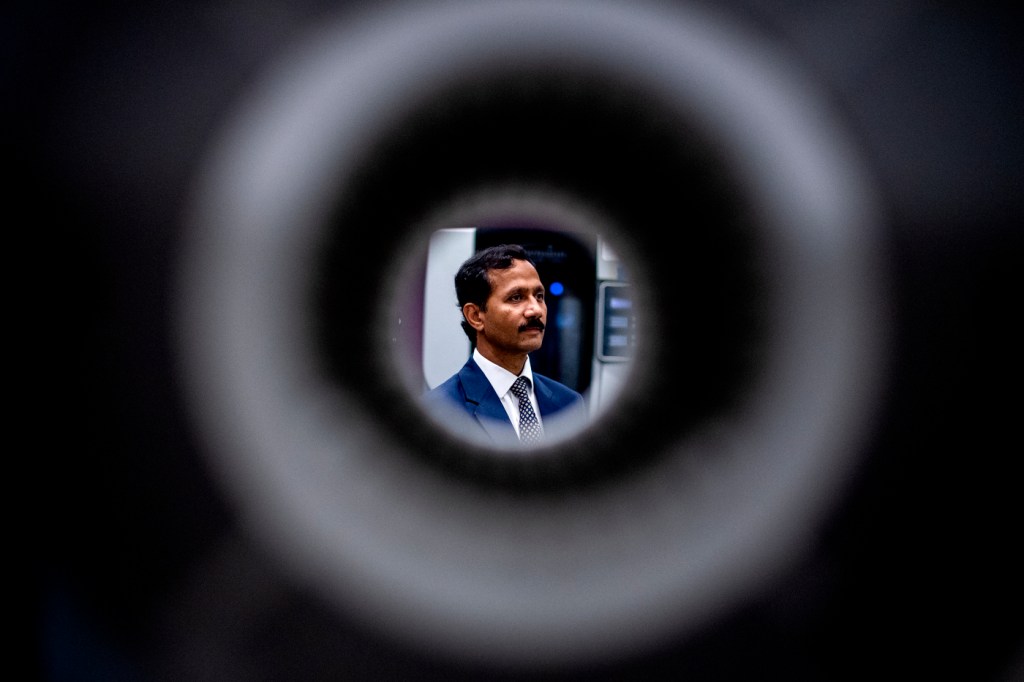
I can come to work and check on my sick dog at home with a video app on my smartphone thanks to the internet of things, which is built on the key idea that machines and everyday devices are always connected and talking to each other to make our lives easy.
That same key idea is driving a new industrial revolution, Industry 4.0. The movement involves next-generation manufacturing machines that use cloud technologies and advanced software platforms to check themselves for errors and performance and, ultimately, make products better and smarter.
But as the manufacturing world undergoes this massive change, people working in this industry are struggling to keep up with the skills new machines require, says Sagar Kamarthi, a professor of mechanical and industrial engineering at Northeastern. And as with revolutions happening in other fields, he says, we need to be prepared for this one.
“If we don’t, we will be far behind every industrialized country,” Kamarthi says. “We won’t be able to maintain global manufacturing competitiveness without developing advanced technologies and training our workforce for these technologies.”
To stay ahead of the curve, a team of Northeastern researchers led by Kamarthi is developing courses to help people working in manufacturing modernize and retool their skills. With a $2 million grant from the National Science Foundation, Kamarthi will direct the Integrative Manufacturing and Production Engineering Education Leveraging Data Science program to develop and test training tools and programs over the course of three years.
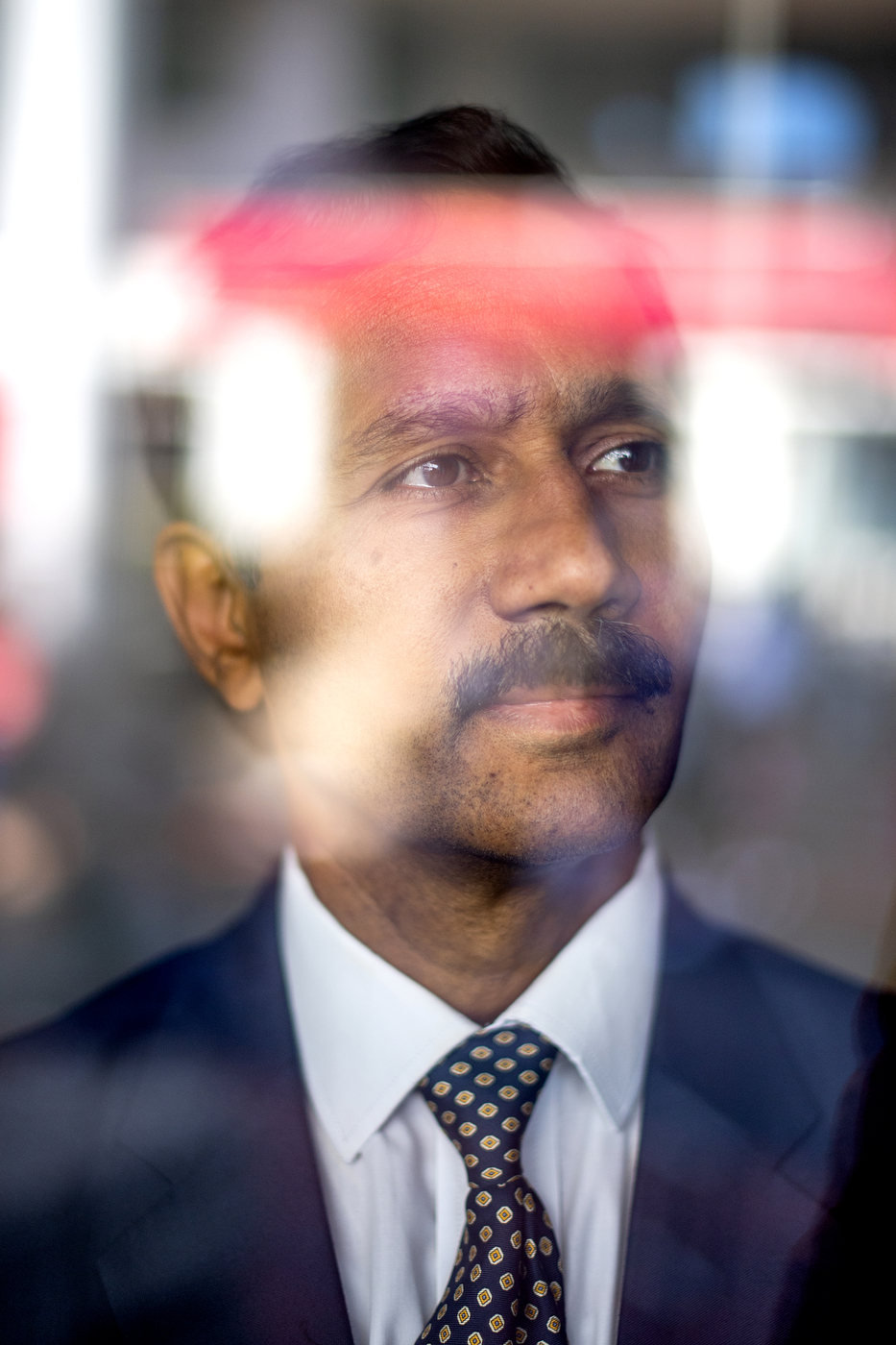
Kamarthi says data science can enable manufacturing machines to diagnose, correct, and ultimately protect themselves to avoid catastrophic breakdowns. Photo by Matthew Modoono/Northeastern University
Several other researchers in data science, digital learning, and manufacturing engineering at Northeastern will be assisting with the work, including Jacqueline Isaacs, professor and interim dean in the College of Engineering; Kemi Jona, assistant vice chancellor for digital innovation and enterprise learning; and Xiaoning Jin and Mohsen Moghaddam, assistant professors of mechanical and industrial engineering.
The courses that they develop will be freely available through online classroom systems to professionals in manufacturing. And, Kamarthi says, Northeastern students, staff, and working professionals will also have access to coursework and certificates applied to data science and smart manufacturing.
Kamarthi, who also directs the College of Engineering’s graduate program in data analytics engineering, develops algorithms that make it easier for machines to diagnose their own systems for errors and predict future failures. His work centers on manufacturing environment, but, he says, these algorithms can be applied to other fields, particularly healthcare and medicine.
In smart manufacturing, sensors can help computers “listen” to various moving parts in a machine or device, such as bearings or spindles, that might signal early symptoms of failure and breakdowns. That means machines at the shop floor level can analyze sensor data and learn on the fly to improve on how they monitor for warning signals, all without the help of people.
“The key is to diagnose based on changes in the vibrations or other signatures that components in a machine generate to predict its health condition,” Kamarthi says. “Then we can plan to replace it timely, and we can avoid catastrophic failures in the operation of machines, such as jet engines and computer servers.”
As he develops these algorithms to process data autonomously, Kamarthi is providing information that engineers and technicians can use to make smart and resilient machines. But that means manufacturing is no longer operating in the same fashion, and people working with these machines will need to catch up with the technology.
That’s why Kamarthi says it is important for him and his team to come full circle in their research and, in addition to developing the programs that will help modernize manufacturing, also help workers in the industry to keep up with the fast technological advances happening around them.
It’s not so much a choice, as it is what needs to be done, Kamarthi says.
“Industry 4.0 is a brand-new technology, so it is not reasonable to expect people who entered the workforce 15 or 20 years ago to be knowledgeable about it,” he says. “But they need to be, because that’s where the field is going, how technology is going to change.”
For media inquiries, please contact media@northeastern.edu.